Blog
The History and Evolution of Spinning Mills
Introduction
Spinning mills have played a crucial role in shaping the textile industry, transforming fiber into yarn and fueling the growth of fabric production worldwide. The evolution of spinning mills has been marked by groundbreaking innovations, from manual spinning techniques to highly automated and smart manufacturing processes.
Today, industry leaders like LMW continue to drive advancements in spinning technology, ensuring efficiency, sustainability, and superior yarn quality. Understanding the journey of spinning mills provides valuable insights into how the industry has reached its present state and where it is headed.
Early Origins: Hand Spinning to the Spinning Wheel
Before the industrial revolution, spinning was a labor-intensive, manual process. Early civilizations used drop spindles, simple tools that twisted fibers into yarn. The invention of the spinning wheel around the 11th century significantly increased productivity, making yarn production faster and more consistent. This innovation laid the foundation for the mechanized spinning industry that followed.
The Industrial Revolution: Birth of Spinning Mills
The late 18th century marked a turning point with the advent of the Industrial Revolution, particularly in Britain. Key inventions transformed the textile industry:
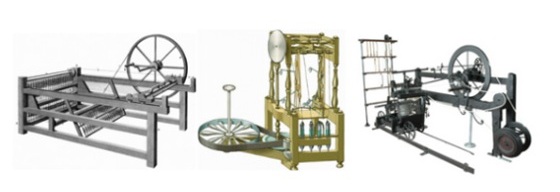
Spinning Jenny (1764): Invented by James Hargreaves, this multi-spindle machine allowed a single operator to spin multiple threads at once
Water Frame (1769): Developed by Richard Arkwright, this machine used water power to produce stronger, finer yarn
Spinning Mule (1779): Samuel Crompton’s innovation combined the best features of the Spinning Jenny and Water Frame, producing high-quality yarn suitable for fine textiles
These inventions led to the establishment of the first spinning mills, where mechanized processes significantly increased yarn production, fueling the expansion of the textile industry.
The 19th and 20th Century: Growth and Global Expansion
During the 19th century, spinning mills became widespread across Europe and North America. The introduction of steam power further enhanced productivity, allowing mills to operate independently of water sources. By the late 19th and early 20th centuries, electrification revolutionized spinning mills, making them more efficient and safer.
The textile industry also expanded beyond Europe, with countries like India, China, and Japan establishing large-scale spinning mills. India, with its rich cotton-growing heritage, became a major player in the textile sector. Among the pioneers, LMW emerged as a leading textile machinery manufacturer, helping modernize India’s spinning industry with cutting-edge technology.
The Modern Era: Automation and Smart Manufacturing
Today, spinning mills have embraced automation and digitalization, reducing reliance on manual labor and improving efficiency. Key advancements include:
IoT-Enabled Machines: Sensors monitor real-time machine performance, enabling predictive maintenance.
AI-Driven Quality Control: Automated systems detect defects faster and with greater accuracy than manual inspections.
Energy-Efficient Spinning: Sustainable practices, such as renewable energy sources and water recycling, have become standard in modern spinning mills.
Ring frame Auto Piecer (RAP)
The fully automated yarn piecing system for ring spinning machine, receives information on yarn break through YBS (Yarn Break Sensor) and travels to the particular spindle and automatically pieces the yarn instantly.
LMW’s RAP is a state-of-the-art automation solution designed to reduce manpower by up to 50%, significantly enhancing operational efficiency. With a shorter auto piecing cycle time and a piecing rate of up to 60 per hour, it ensures seamless and precise piecing for improved yarn quality. The system maximizes productivity, achieving an efficiency of over 85%, making it a highly reliable automation tool for modern spinning operations.
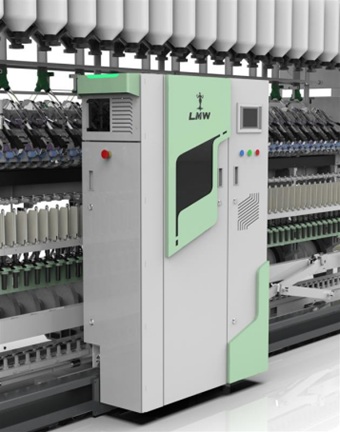
Card with Drafting System (CDS)
CDS (Card with Drafting System) offers a significant advancement by allowing the process to skip the draw frame. This system integrates the drafting process directly with the carding machine, which helps in maintaining consistent sliver quality and optimizing overall performance.
LMW’s Card LC636 SX with CDS helps achieve consistent quality with higher precision, seamless production and higher output with CDS (Card with Drafting system) which is a game changer in the preparatory spinning process for Airjet spinning.
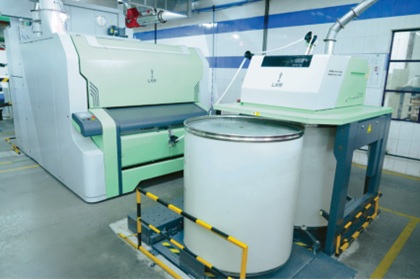
LMW RESPIN Impact
As the textile industry moves towards a more sustainable future, circularity has become a key focus. With the growing global demand for eco-friendly practices, LMW is at the forefront of this transformation, offering innovative solutions for recycled fiber processing. LMW RESPIN is a commitment to a sustainable future. It is designed to integrate sustainability, innovation, and performance, enabling textile manufacturers to adopt eco-friendly practices. Various raw materials / feed materials are used in the recycled process. Virgin material of cotton and polyester are added as per the end product requirements.
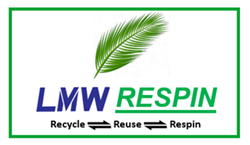
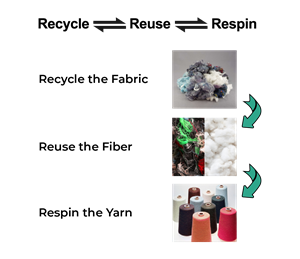
“Recycle, Reuse, Respin”: LMW’s Mantra for a Greener Future
4S – Sustainable Smart Solution for Spinning Success
Here are LMW’s latest smart spinning machinery solutions, designed to enhance productivity, sustainability, and automation in modern spinning mills.
Product | Model |
Gentle Blowroom | Automatic Bale Plucker LA23/S |
Varioclean LB9/2 | |
Unimix LB7/4, Unimix 7/6 | |
Flexiclean LB5/6 | |
Supremoclean LB10/2 | |
Card | Card LC363/361 S |
Card LC636/SX | |
Draw Frame | Breaker Draw frame LDB3 Series |
Finisher Draw frame LDF3 | |
Finisher Draw frame LDF3 2S (Twin Delivery) | |
Lap Former | LH20 S |
Comber | LK69 S/M |
Speed Frame | LF4280 Series |
Ring Frame | LRJ 9 Series |
Compact Spinning | SPINPACT |
Autowinder | Lakshmi Auto Winder LAW60 |
Automation Solutions |
Blending Solution – Autoblend LA10 |
Card with Drafting System – CDS |
Lap Transportation System – LTS |
Roving Transportation System – RTS |
Yarn Breakage Sensor / Roving Stop Motion – YBS / RSM |
Ring frame Auto Piecer – RAP |
Cone Transportation System – CTS |
Mill Network System – Spin Connect |
Conclusion
The journey of spinning mills—from hand spinning to AI-driven automation—reflects the continuous pursuit of efficiency and quality in textile manufacturing. As the industry advances, modern spinning mills will play a key role in shaping the future of global textiles, ensuring sustainable and high-performance production for generations to come.
Today, LMW’s smart spinning solutions continue to shape the future of textile manufacturing, blending technological advancements with a commitment to sustainability and efficiency. As spinning mills embrace technology, LMW remains a trusted partner, driving the next phase of evolution in the textile industry.